Here, We provide MSM GTU Paper Solution Winter 2021. Read the Full Material Science And Metallurgy gtu paper solution given below.
(a) Differentiate between macro and micro examinations
Macro Examination | Micro Examination |
---|---|
Observation of large-scale features | Observation of small-scale features |
Examines the overall appearance of a sample | Examines the internal structure and composition of a sample |
Can be performed with the naked eye | Usually requires the use of a microscope |
Used to identify gross abnormalities or defects | Used to identify fine details and subtle variations |
Examples: Inspection of large mechanical parts, visual inspection of buildings | Examples: Microscopic examination of metals and polymers, examination of cells and tissues |
(b) Define: (1) Toughness (2) Hardness (3) Hardenability (4) Malleability
Toughness is the total amount of energy absorbed by the material before its failure.
Hardness is a measure of a material’s resistance to permanent deformation, indentation, or scratch.
Hardenability is a measure of a material’s ability to be hardened by heat treatment.
Malleability is a measure of a material’s ability to be deformed plastically without breaking.
(c) Discuss selection criteria for materials used in engineering applications.
Availability of materials
The materials which are available readily and in abundance in the market should be selected.
As far as possible, the materials which are not available easily should be avoided.
Cost of material
In today’s world of competition, cost plays a significant role in the success of the product.
The material should be selected such that the total cost should be minimum and within the specified limit.
The total cost includes the cost of material and the cost of processing the material.
Manufacturing considerations
The manufacturing considerations play a vital role in material selection. The selected material should be suitable for the required manufacturing processes.
For example, if the body of the machine is to be made by the casting process, the material suitable for the casting process must be selected.
However, if the material is found suitable for all other considerations, sometimes the manufacturing process can be changed, if feasible.
Material properties
The material properties, in general, and mechanical properties, m particular, govern the selection of the materials.
The different mechanical properties considered are static strength, fatigue strength, stiffness, elasticity, plasticity, ductility, brittleness, malleability, hardness, toughness, resilience, creep, etc.
(a) Explain a atomic packing factor
The atomic packing factor (APF) is a dimensionless quantity used to describe the arrangement of atoms in a crystalline solid.
It is defined as the fraction of the total volume of a unit cell occupied by its atoms. The APF provides a measure of the degree of close packing of the atoms in a crystalline solid and is an important factor in determining the properties of the material.
The APF is a fundamental property of a material and is determined by the crystal structure, the size and shape of the atoms, and the interatomic distances between the atoms.
For example, the APF of simple cubic structures is 0.52
(b) Calculate the APF for BCC and FCC structures.
APF in FCC Structure is
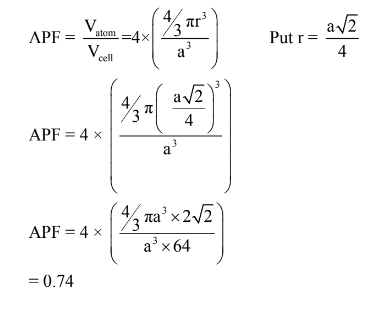
APF in BCC Structure is
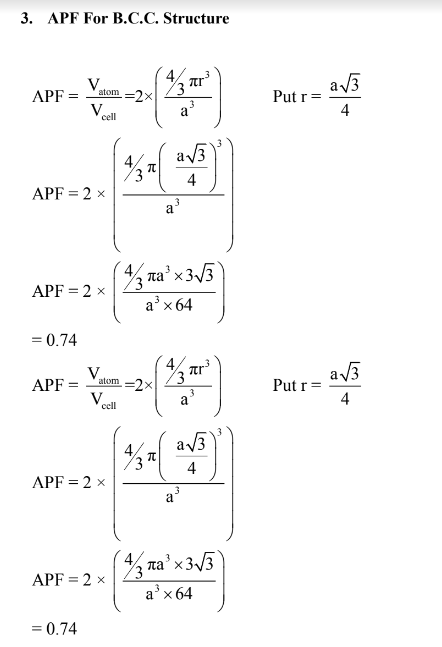
(c) Discuss mechanisms of quenching of steel. State the advantages and drawbacks
of water & oil as quenching media.
Quenching is a heat treatment process in which steel is rapidly cooled from an elevated temperature to below its critical temperature. The rapid cooling rate promotes the formation of a martensitic microstructure, which is hard and strong. There are several mechanisms involved in the quenching of steel, including the transformation of austenite to martensite, the precipitation of hard carbides, and the solidification of the microstructure.
Water and oil are two common quenching media used in the heat treatment of steel. Each has its own advantages and drawbacks:
Water:
- Advantages: Water is a very effective quenching medium because it can rapidly cool the steel, promoting the formation of a martensitic microstructure. Water is also relatively inexpensive and readily available.
- Drawbacks: Water has a tendency to cause thermal shock, which can lead to cracking or warping of the steel. Water also corrodes the steel, which can lead to the formation of surface defects.
Oil:
- Advantages: Oil is a slower quenching medium than water, which reduces the risk of thermal shock and cracking. Oil also has a higher flash point than water, which makes it a safer option for quenching. Oil can also be used to selectively quench different areas of the steel at different rates, allowing for more precise control of the final microstructure.
- Drawbacks: Oil is more expensive than water, and it can also be more difficult to obtain. Oil is also less effective than water at promoting the formation of a martensitic microstructure, so the quenching rate may need to be increased in order to achieve the desired results.
[or] (c) Explain the different methods for Grain size measurement.
There are several methods for measuring the grain size of a metal or other material, including the following:
Optical Microscopy: This is the most widely used method for measuring grain size in metals. It involves the use of an optical microscope to observe the microstructure of a material and to measure the size and shape of the individual grains. The grain size can be measured either directly, by measuring the longest dimension of the grain, or indirectly, by using a standard chart or formula to convert the observed structure into an equivalent grain size.
Image Analysis: This method involves the use of computer software to analyze digital images of the microstructure of a material. The software can be used to automatically identify and measure the size of the individual grains, and to generate a histogram of the grain size distribution.
X-ray Diffraction: This method involves the use of X-rays to study the crystal structure of a material. X-ray diffraction can be used to determine the average grain size of a material, based on the spacing of the lattice planes within the crystal structure.
Electron Microscopy: This method involves the use of an electron microscope to observe the microstructure of a material at high magnification. Electron microscopy can be used to directly measure the size and shape of the individual grains, and to generate a detailed image of the microstructure.
Line Profile Analysis: This method involves the use of a line profile analysis technique to determine the average grain size of a material. Line profile analysis involves collecting data along a line within the microstructure and analyzing the data to determine the average grain size.
(a) What is phase diagram?
A phase diagram is a graphical representation of the conditions under which different phases of a material exist in equilibrium.
It provides information about the relationships between temperature, pressure, and composition for a particular system.
A phase diagram typically consists of a number of phase boundaries that separate the different phases and a critical point, which marks the conditions at which the material transitions from one phase to another.
The phase diagram provides a visual representation of the behavior of a material under different conditions and can be used to predict its properties and performance.
(b) Explain Lever rule.
The Lever Rule is a simple empirical rule used to calculate the composition of a solid solution in a two-phase system at equilibrium. The rule is based on the concept of leverages and applies to binary solid solutions, where two solids are in mutual solid solution.
The Lever Rule states that the fraction of each solid in a two-phase system is proportional to the ratio of the distances from the tie-line to the end of the respective solid in the phase diagram. This can be expressed mathematically as follows:
X1 / X2 = (V2 - Vf) / (Vf - V1)
where X1 and X2 are the mole fractions of solids 1 and 2, respectively, Vf is the volume fraction of the solid solution, and V1 and V2 are the volumes of solids 1 and 2, respectively.
The Lever Rule can be used to determine the composition of a solid solution in a two-phase system, given the composition of the end-members and the location of the tie-line in the phase diagram. It is a useful tool for understanding the behavior of solid solutions under different conditions and for predicting the composition of materials in various industrial processes.
(c) What is Gibb’s phase rule? Define system, phase and degree of freedom. Show
that the degree of freedom at eutectic point in a binary phase diagram is zero.
Gibb’s phase
Gibbs’ phase rule is a thermodynamic principle that relates the number of phases in a system to the number of intensive variables that can be varied while still maintaining phase equilibrium. It provides a fundamental understanding of the behavior of a system under various conditions and is widely used in materials science, thermodynamics, and chemical engineering.
The Gibbs’ phase rule is formulated as follows:
F = C – P + 2
where F is the number of degrees of freedom, C is the number of components in the system, and P is the number of phases.
System: A system is a collection of matter or energy that is isolated from its surroundings. In thermodynamics, a system is defined as a region of space that is separated from its surroundings by a well-defined boundary.
Phase: A phase is a region within a system that is physically and chemically homogeneous. A phase is characterized by its own set of physical and chemical properties, such as its density, thermal conductivity, and chemical composition.
Degree of Freedom: A degree of freedom is an intensive variable (such as temperature or pressure) that can be varied independently of the other variables in a system while still maintaining phase equilibrium. The number of degrees of freedom in a system is determined by the number of independent variables that can be varied, and it is a measure of the number of possible states of the system.
At the eutectic point in a binary phase diagram
there is only one phase present, which is a mixture of the two components. The temperature and composition are fixed at the eutectic point, so there is only one degree of freedom (pressure).
Therefore, at the eutectic point in a binary phase diagram, the degree of freedom is zero
F = C – P + 2 = 2 – 1 + 2 = 3 – 1 + 2 = 0
(a) What is significance of soaking time provided in annealing or hardening?
The soaking time provided during annealing or hardening is a critical factor that determines the quality and performance of the final product. Soaking time refers to the amount of time that the metal is maintained at a constant temperature during a heat treatment process.
In annealing, the purpose of soaking is to ensure that the entire metal object is heated to a uniform temperature and held at that temperature for a sufficient amount of time to allow the grains of the metal to recrystallize and homogenize.
In hardening, the purpose of soaking is to ensure that the entire metal object is heated to the proper temperature for a sufficient amount of time to allow the metal to transform from a ferritic or austenitic structure to a martensitic structure.
(b) What is a eutectic, eutectoid and peritectic reaction.
Eutectic Reaction: A eutectic reaction is a type of phase change in which a mixture of two or more solid phases transforms into a single solid phase with a lower melting point than any of the original solid phases. The new solid phase is called a eutectic mixture and has a composition that is intermediate between the original solid phases. Eutectic reactions are commonly observed in binary solid solutions, where two solids are in mutual solid solution.
Eutectoid Reaction: A eutectoid reaction is a type of phase change in which a single solid phase transforms into two or more solid phases with different compositions and properties. The new solid phases are called eutectoids and are typically mixtures of different solid phases that were present in the original solid phase. Eutectoid reactions are commonly observed in iron-carbon alloys, where the austenite phase transforms into pearlite and ferrite phases.
Peritectic Reaction: A peritectic reaction is a type of phase change in which a liquid phase transforms into a solid phase and a solid phase transforms into a liquid phase. The new solid phase has a composition that is intermediate between the liquid and solid phases, and the new liquid phase has a composition that is intermediate between the original liquid and solid phases. Peritectic reactions are commonly observed in ternary phase diagrams, where three phases are in mutual solid solution.
(c) Draw iron- carbon diagram and mention all major elements.
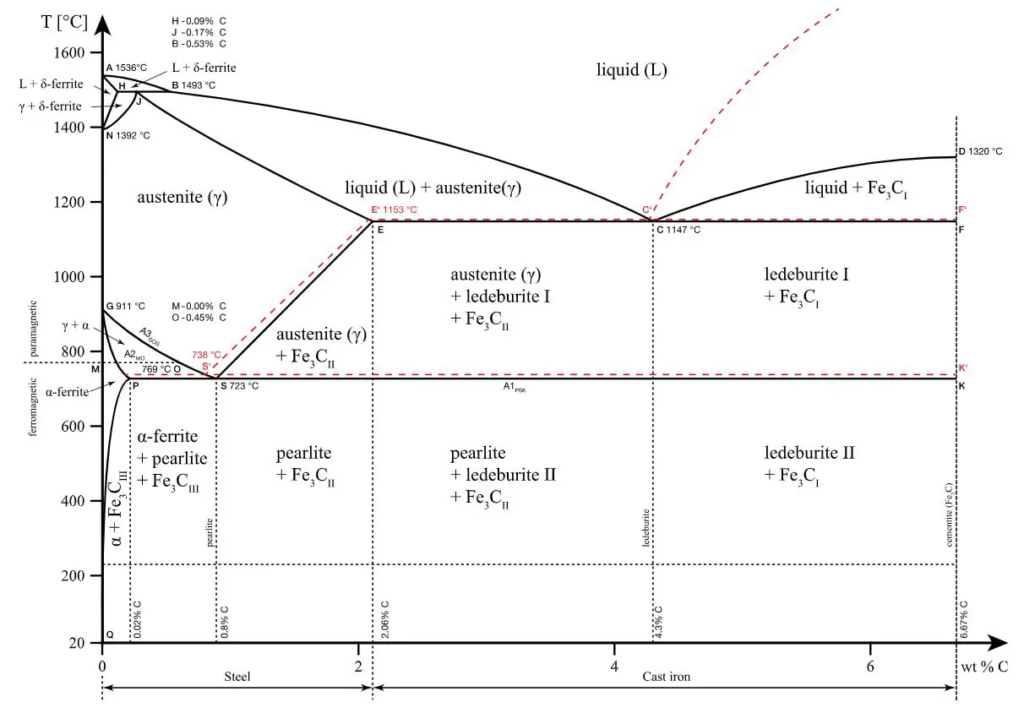
(a) Write in brief: Hastelloy material
Hastelloy is a group of high-performance nickel-based alloys that have excellent resistance to corrosion and high-temperature oxidation.
They are used in a variety of industrial applications including chemical processing, nuclear reactors, and pollution control.
The unique composition of Hastelloy provides superior resistance to various forms of corrosion, including stress corrosion cracking, pitting, and crevice corrosion.
(b) Give a few applications of copper alloys.
Copper alloys are used in a wide range of applications due to their good electrical and thermal conductivity, high strength-to-weight ratio, and resistance to corrosion. Some common applications of copper alloys include:
- Electrical wiring and connectors, due to their conductivity and resistance to corrosion.
- Coins, due to their durability and resistance to corrosion.
- Architectural applications, such as roofing, flashing, and gutters, due to their beauty and durability.
- Automotive components, such as radiators and heat exchangers, due to their thermal conductivity and ability to withstand high temperatures.
- Marine applications, such as ship propellers and marine fittings, due to their resistance to corrosion in seawater.
- Industrial machinery components, due to their strength and ability to withstand wear and tear.
(c) Describe effect of quenching media on properties of steel during heat treatment.
Quenching is a process used in heat treatment of steel to rapidly cool the material from its austenitizing temperature to a temperature below its critical range. The choice of quenching media (air, oil, water, etc.) can greatly impact the properties of the steel after quenching.
- Water: Quenching in water provides the fastest cooling rate and is used for high-carbon steels. This results in a hard, brittle martensitic structure.
- Oil: Quenching in oil provides a slower cooling rate compared to water and is used for lower carbon steels. This results in a harder and more uniform structure compared to air-cooling, but with increased toughness.
- Air: Air-cooling provides the slowest cooling rate and is used for low carbon steels. This results in a softer and less uniform structure compared to oil-quenching, but with increased ductility.
- Salt baths: Quenching in salt baths provides a controlled and uniform cooling rate. This results in a structure with improved dimensional stability and uniform hardness.
Therefore, the choice of quenching media will depend on the desired properties for a particular application and the specific type of steel being used.
(a) What is the main objectives of NDT method?
The main objectives of Non-Destructive Testing (NDT) methods are:
- To detect and locate surface and sub-surface defects, discontinuities, or other anomalies that could affect the performance or safety of a component or structure.
- To determine the dimensions, thickness, or other physical properties of a component or structure without causing damage.
- To evaluate the integrity, quality, and reliability of a component or structure, and ensure that it meets relevant standards and specifications.
- To monitor the effects of corrosion, fatigue, and other forms of degradation over time and provide information on the remaining life and reliability of a component or structure.
- To support predictive maintenance and extend the service life of components and structures.
(b) Explain briefly the two methods of finding carbon percentage in steels.
There are two methods of determining the carbon content in steels:
- Spectroscopic analysis: This method involves analyzing the steel sample using spectroscopy techniques such as Optical Emission Spectroscopy (OES) or Inductively Coupled Plasma (ICP) Spectroscopy. The sample is atomized and the light emitted from the sample is analyzed to determine the elemental composition, including the carbon content.
- Chemical analysis: This method involves performing a chemical reaction on the steel sample to determine its carbon content. A commonly used method is the combustion analysis, where the sample is burned and the resulting gases are analyzed to determine the carbon content. Another method is the gravimetric analysis, where the sample is reacted with a reagent to form a compound with a known carbon content, and the carbon content is determined by weighing the resulting compound.
(c) Explain the effect of Grain size on the properties of metals.
The grain size of a metal has a significant effect on its properties, including:
- Strength: Smaller grain sizes generally lead to increased strength and hardness due to the increased number of grain boundaries, which act as obstacles to dislocation motion.
- Ductility: Larger grain sizes generally lead to decreased ductility and toughness, as larger grains can more easily fracture under stress.
- Toughness: Smaller grain sizes generally lead to increased toughness, as the increased number of grain boundaries can absorb more energy before fracture.
- Corrosion resistance: Smaller grain sizes can increase the corrosion resistance of a metal as the smaller grain boundaries act as physical barriers to the diffusion of corrosive agents into the metal.
- Thermal conductivity: Larger grain sizes generally lead to increased thermal conductivity, as the larger grains can conduct heat more effectively.
- Electrical conductivity: The grain size has little effect on the electrical conductivity of a metal.
(a) Explain cathodic protection against corrosion
Cathodic protection is a technique used to prevent corrosion of metal structures, such as pipelines, tanks, and ships, by making them the cathode of an electrochemical cell.
The principle of cathodic protection is based on the fact that corrosion is an electrochemical process that occurs when metal is oxidized to form metal ions. By applying a low voltage direct current (DC) to the metal structure, cathodic protection causes the metal to become the cathode, rather than the anode, in the electrochemical reaction.
This causes the flow of electrons to be directed away from the metal structure and towards a more easily oxidized material, such as a sacrificial anode or an impressed current source.
Cathodic protection can be a very effective way to prevent corrosion, but it must be designed, installed, and monitored carefully to ensure that it is working properly. Improper design or maintenance of cathodic protection systems can actually increase the rate of corrosion, rather than preventing it.
(b) Explain any one methods for production of metal powders.
Reduction process
In the Reduction process, the compounds of metals (usually oxides, e.g., iron oxide)are reduced with CO or H2 at temperatures below the melting point of the metal (e.g., iron) is an atmosphere-controlled furnace. The reduced product is then crushed and ground.
Sponge-iron powder is produced this way.
Fe3O4 + 4C = 3Fe + 4CO
Fe3O4 + 4CO = 3Fe + 4CO2
The copper powder can be produced by the same method i.e., by heating copper oxide in a stream of hydrogen,
Cu2O + H2 = 2Cu + H2O
Powders of W, Mo, Ni, and CO are also manufactured by the reduction process. The reduction process is a convenient, economical and flexible method and perhaps the largest volume of metallurgical powders is made by the process of oxide reduction.
(c) What is powder metallurgy? State the applications of powder metallurgy.
Powder metallurgy is an art and science of producing fine metal powders and then making objects from the individual, mixed or alloyed metal powders with or without the inclusion of non-metallic constituents.
Aapplications of powder metallurgy.
- Porous products, e.g., bearings and filters.
- Refractory parts, e.g., components made out of Tungsten, Tantalum, and Molybdenum are used in electric bulbs, radio valves, oscillator valves, X-ray tubes in the form of filament, cathode, anode, control grids, etc.
- Products of complex shapes that require considerable machining when made by other processes, e.g., toothed components such as gears.
- Automotive components such as electrical contacts, crankshaft drive or camshaft sprocket, piston rings and rocker shaft brackets, door mechanisms, connecting rods, and brake linings, etc.
- Products made from materials that are very difficult to machine, e.g., tungsten carbide, etc.
- Components are gauges, wire drawing dies, wire guides, deep drawing, stamping and blanking tools, stone hammers, rock drilling bits, etc.
- Products where the combined properties of two metals or of metals and non – metals are desired: non-porous bearings, electric motor brushes, etc.
- Atomic energy applications.
Tungsten parts are employed in plasma jet engines, etc., which are operated at about 1850°C. Silver infiltrated tungsten is used in nozzles for rockets and missiles. Use as parts in military and defense systems, e.g., in military arms. - Parts made by powder metallurgy have also been used in clocks and timing devices, typewriters, adding machines, calculators, permanent magnets, laminated bimetallic strips, etc.
- Grinding wheels that incorporate steel and diamond powder may be manufactured by powder metallurgy.
(a) Draw Jominy hardenability set-up including labeling & important dimensions.
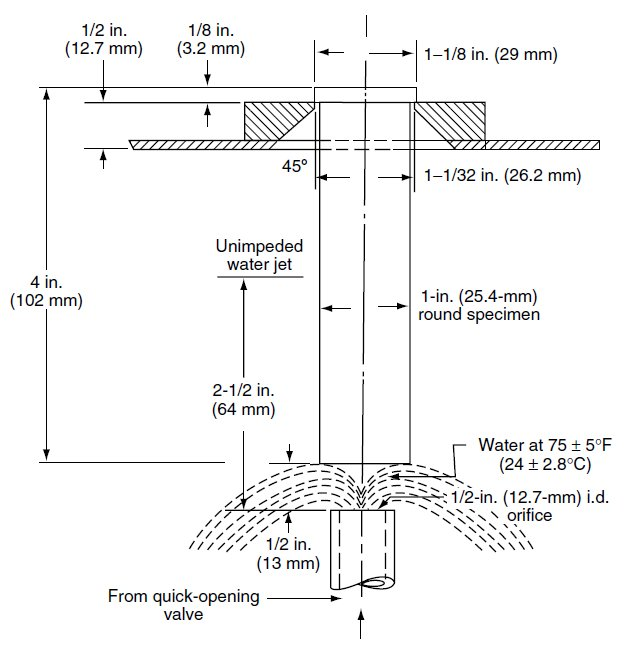
(b) Explain difference between dry type and Wet type corrosion.
Factor | Dry Corrosion | Wet Corrosion |
---|---|---|
Definition | Corrosion that occurs in the absence of moisture | Corrosion that occurs in the presence of moisture |
Characteristics | Typically occurs at high temperatures, low corrosion rate, often caused by oxidation or high-temperature reactions with gases | Typically occurs at low temperatures, high corrosion rate, often caused by electrochemical reactions in the presence of water and oxygen |
Appearance | Typically appears as a uniform layer of oxide on the metal surface | Typically appears as pits or localized areas of corrosion |
Rate of Corrosion | Low | High |
(c) Explain the NDT method widely used for inspection of castings.
There are several different non-destructive testing (NDT) methods that can be used for inspection of castings. The most widely used NDT method for inspecting castings is radiographic testing, also known as X-ray inspection.
In radiographic testing, X-rays are passed through the casting, and the resulting image is captured on film or digital media. The X-rays penetrate the metal, and any defects or voids within the casting appear as dark areas on the image. Radiographic testing can detect a wide range of defects, including porosity, cracks, inclusions, and other discontinuities that may not be visible on the surface of the casting.
Another commonly used NDT method for inspecting castings is ultrasonic testing. In ultrasonic testing, high-frequency sound waves are transmitted into the casting, and the time it takes for the waves to travel through the metal and return is measured. Any defects or voids within the casting will cause a change in the time it takes for the waves to return, and this can be used to identify the presence of defects.
Magnetic particle inspection and liquid penetrant inspection are two other NDT methods that are sometimes used for inspecting castings. In magnetic particle inspection, a magnetic field is applied to the casting, and iron oxide or iron oxide-coated magnetic particles are introduced to the surface. The particles will be attracted to any defects or discontinuities in the metal, making them visible. In liquid penetrant inspection, a liquid penetrant is applied to the surface of the casting, and the penetrant is drawn into any defects or discontinuities. The excess penetrant is then removed, and a developer is applied to make the penetrant visible, revealing the location of any defects.
The specific NDT method that is used for inspection of castings will depend on the type of casting being inspected, the size and location of the defects being sought, and the specific requirements of the inspection.
Read More : KTM GTU Paper Solution Winter 2021
Read More : Indian Constitution GTU Paper Solution Winter 2021
“Do you have the answer to any of the questions provided on our website? If so, please let us know by providing the question number and your answer in the space provided below. We appreciate your contributions to helping other students succeed.